
La gestión visual es una técnica de gestión empresarial que comunica información importante en el lugar de trabajo físico. Es un sistema de pantallas de información, controles visuales, etiquetas y señales, códigos de colores y otras marcas en lugar de instrucciones escritas. Las organizaciones Lean recurren en gran medida a la gestión visual para detectar anomalías y reforzar las normas, al tiempo que garantizan la estabilidad y la seguridad en el lugar de trabajo. Lo ideal es que todo el mundo pueda evaluar el estado de una situación de un vistazo, incluso el observador casual. Los empleados también necesitan pantallas visuales que muestren lo que se espera de ellos y que les mantengan informados sobre el estado de la producción y las necesidades de los clientes.
Un sistema de gestión visual eficaz trata de mostrar el estado de la producción y la información sobre el rendimiento, comunicar las normas y las instrucciones de trabajo, hacer que los problemas y las anomalías sean lo más evidentes posible y mostrar la identidad y las direcciones. Puede reducir la posibilidad de que se produzcan errores de comunicación, pone de manifiesto las anomalías y desviaciones y proporciona una visión inmediata de lo que hay que hacer a continuación. Cuando los problemas y las desviaciones son visibles y evidentes para todos, se pueden tomar medidas correctivas inmediatas para aumentar la eficiencia y la eficacia de los procesos. Los controles visuales también se utilizan para compartir objetivos e ideas, informar del progreso del equipo y del Kaizen, e indicar los riesgos de seguridad y promover un comportamiento seguro en el trabajo.
Las investigaciones demuestran que las personas tienden a aprender y procesar la información más visualmente. Por lo tanto, las comunicaciones visuales eficaces pueden tener un impacto en la seguridad, la productividad, el coste, la calidad, la entrega a tiempo, el inventario y la fiabilidad del equipo. Los elementos visuales en el lugar de trabajo pueden desempeñar un papel importante en la formación laboral, lo que eliminará la necesidad de una supervisión constante. Los empleados identificarán y reaccionarán rápidamente a los problemas de seguridad, calidad y eficiencia. La gestión visual ofrece otros beneficios, entre los que se incluyen:
- Crea estabilidad en el entorno, el equipo y el trabajo realizado.
- Reduce los errores y equivocaciones.
- Reduce el tiempo de inactividad y los costes de mantenimiento.
- Aumenta la concienciación sobre la gestión de residuos y desechos.
- Mejora el cumplimiento de la seguridad.
- Mejora la comunicación entre los distintos turnos.
- Mejora la participación y la moral de los empleados.
- Elimina la necesidad de reuniones que consumen mucho tiempo.
- Refuerza la mejora continua.
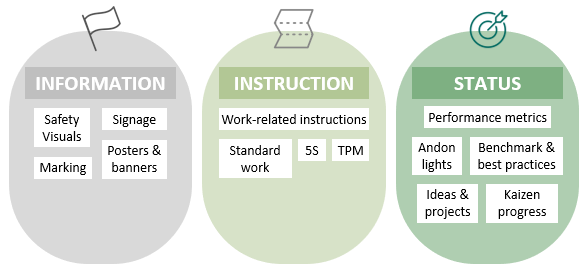
Muchas técnicas y principios de Lean se basan en la gestión visual, empezando por la señalización del suelo mediante cintas adhesivas hasta las grandes pantallas visuales y los marcadores. La gestión visual es la fuerza clave que sustenta muchas técnicas lean populares, como las 5S, el trabajo estándar, el mantenimiento productivo total (TPM), el cambio rápido y la producción «pull». Es especialmente importante durante la fase inicial de la implantación de Lean, cuando las empresas utilizan conceptos como las 5S y el TPM para crear normas y establecer una estabilidad operativa.
- Las 5S son uno de los principios más fundamentales de Lean. Implica muchas actividades visuales que pueden ayudar a crear un mejor ambiente de trabajo. Sugiere el uso de colores y etiquetas para marcar claramente las ubicaciones de almacenamiento de cada artículo en el lugar de trabajo. También define los niveles de inventario y los desencadenantes de reordenación para garantizar que todo esté disponible cuando se necesite en el punto de uso. Si algo no es normal, queremos hacerlo lo más evidente posible.
- Los visuales TPM simplifican las actividades de mantenimiento preventivo asegurando que los equipos se mantienen en condiciones óptimas de funcionamiento con un mínimo de averías. También pueden utilizarse para identificar y evitar que las anomalías se conviertan en averías. Etiquetar y marcar los manómetros, los niveles de aceite y los puntos de lubricación son ejemplos de controles visuales que permiten a los empleados detectar fácilmente las anomalías y las condiciones fuera de especificación de un vistazo. Deben existir pruebas de la transparencia de los equipos para facilitar su puesta en marcha y comprobación. También se recomienda utilizar registros de averías en cada máquina.
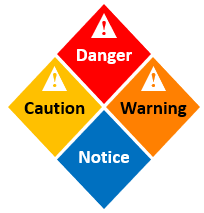
- Los controles visuales de seguridad son importantes para mantener las instalaciones seguras y respetuosas con el medio ambiente. Alertan a los empleados y a los visitantes de los lugares y situaciones potencialmente peligrosas para evitar condiciones inseguras. Es importante identificar correctamente los equipos de protección contra incendios, las duchas de seguridad, las estaciones de lavado de ojos, los equipos de protección personal y los puestos de primeros auxilios. La señalización, las advertencias de peligro y las instrucciones de seguridad deben proporcionarse en el punto de necesidad. Todos los interruptores de desconexión de todos los equipos eléctricos deben estar claramente identificados.
- Un sólido sistema de gestión visual busca promover la coherencia y crear estabilidad en los procesos. Los visuales de trabajo estándar ayudan a garantizar que las tareas sean siempre realizadas por todos de la manera más eficiente y eficaz posible. Incluyen procedimientos, instrucciones de trabajo, hojas de control, listas de comprobación, diagramas de flujo, horarios, fotos y lecciones de un punto. Estos elementos visuales ayudarán a minimizar los errores de producción y garantizarán que todos respeten las normas del lugar de trabajo. Recuerde que los mejores visuales son los que incluyen fotos y/o dibujos y los que se colocan en el punto de necesidad.
Más aplicaciones:
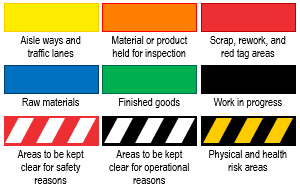
- Marcación del suelo y del sistema de tuberías.
- Marcación de los materiales y productos que se producen.
- Marcar las máquinas, los equipos y las líneas de producción.
- Marcar las oficinas, las salas, las celdas y las áreas de almacenamiento.
- Señales de orientación para ayudar a las personas a encontrar el camino.
- Señales tales como no entrar y señales de no fumar.
- Utilizar tarjetas con códigos de colores y tableros Kanban en un sistema de arrastre.
- Utilización de tableros para priorizar los problemas y comunicar las contramedidas.
- Utilización de carteles y pancartas para reforzar los objetivos y principios Lean.
- Utilización de tableros de seguimiento para facilitar la comunicación en operaciones de varios turnos.
- Utilización de cuadros de mando para comunicar y seguir las métricas del proceso en tiempo real.
- Uso de tableros de resumen de producción para mostrar información como la eficiencia, el tiempo Takt, etc.
Andon y tableros de resumen de producción:
Una pantalla Andon es un sistema de iluminación multicolor que proporciona un mecanismo simple y consistente para comunicar información en el taller. Es una herramienta de comunicación eficaz que llama la atención inmediatamente sobre los problemas que se producen en una máquina o célula de fabricación. El sistema puede incluir medios para detener la producción de manera que se pueda corregir el problema. Por ejemplo, una luz puede encenderse o cambiar de color para indicar una escasez de materias primas o la necesidad de mantenimiento.
Un lugar de trabajo sin una visualización de las métricas de producción es como un coche sin velocímetro. Puede que sepa a dónde va, pero no tiene ni idea de cuándo llegará. Los tableros de resumen de producción se utilizan para supervisar el rendimiento del proceso y ver si satisface la demanda del cliente. Las luces y los tableros de resumen de producción deben ser visibles en el taller para comunicar el estado actual de un sistema de producción. Todo el mundo debería poder ver en qué punto se encuentra la producción, lo que permite a los equipos de mantenimiento y producción resolver rápidamente los problemas de proceso y calidad que puedan surgir durante la producción.
Consejos para crear un sistema de gestión visual cohesivo:
- Recuerde que su objetivo es hacer que el área sea más informativa.
- Determine dónde necesita implementar la gestión visual.
- Decida quiénes van a estar involucrados en el esfuerzo de implementación.
- Identifique los déficits de información, determine lo que necesita ser mostrado y el tipo de información que necesita ser transmitida. Una forma es diseñar una lista de comprobación visual que cubra las ubicaciones de almacenamiento, el trabajo estándar, la seguridad, el mantenimiento, las métricas del proceso, los tableros visuales, etc.
- Marque los suelos, añada señales, etiquete las áreas de almacenamiento, etc. Utilice los estándares de color que se están utilizando de forma consistente en la instalación.
- La información tiene que ser fácilmente comprensible, concisa, precisa, relevante, actualizada y accesible para todos. Todo el mundo tiene que ser capaz de entender el mensaje.
- Crear una guía que describa los elementos clave asociados a cada tipo visual.
Más información:
- La gestión visual no se limita a hacer visibles los gráficos y las métricas en una pared, sino que se trata de una visualización en tiempo real, cada hora o cada día, que permite al equipo responder rápidamente a las señales para resolver problemas o apoyar el proceso de producción. Esto suele generar una sensación de urgencia entre el equipo y permite resolver los problemas en el momento, eliminando posibles complicaciones.
- Las métricas de los procesos deben mostrarse en la máquina o en la célula de fabricación, mientras que la información general de la planta debe publicarse en un lugar central donde todos puedan verla de un vistazo.
- Es muy común realizar eventos Kaizen en los que el objetivo principal es mejorar la visualidad de un área de trabajo específica o de un proceso. Por ejemplo, estabilizar el entorno de trabajo utilizando las 5S, estabilizar cómo se realiza el trabajo utilizando el trabajo estándar, o estabilizar el rendimiento y la fiabilidad de los equipos utilizando el TPM.