
Visual Management è una tecnica di gestione aziendale che comunica informazioni importanti sul posto di lavoro fisico. È un sistema di display di informazioni, controlli visivi, etichette e cartelli, codifica dei colori e altri contrassegni al posto delle istruzioni scritte. Le organizzazioni Lean fanno molto affidamento sulla gestione visiva per individuare le anomalie e rafforzare gli standard, assicurando allo stesso tempo stabilità e sicurezza sul posto di lavoro. Idealmente, tutti dovrebbero essere in grado di valutare lo stato di una situazione a colpo d’occhio, anche l’osservatore casuale. I dipendenti hanno anche bisogno di display visivi che mostrino cosa ci si aspetta da loro e che li tengano informati sullo stato della produzione e sulle esigenze dei clienti.
Un sistema efficace di gestione visiva cerca di visualizzare lo stato della produzione e le informazioni sulle prestazioni, comunicare gli standard e le istruzioni di lavoro, rendere i problemi e le anomalie il più evidenti possibile e mostrare identità e direzioni. Può ridurre l’opportunità di cattiva comunicazione, evidenzia le anomalie e le deviazioni e fornisce una visione immediata di ciò che deve essere fatto dopo. Quando i problemi e le deviazioni sono visibili ed evidenti a tutti, si possono intraprendere azioni correttive immediate per aumentare l’efficienza e l’efficacia dei processi. I controlli visivi sono anche usati per condividere obiettivi e idee, riportare i progressi del team e del Kaizen, indicare i rischi per la sicurezza e promuovere un comportamento sicuro sul lavoro.
La ricerca dimostra che le persone tendono ad apprendere ed elaborare le informazioni in modo più visivo. Pertanto, comunicazioni visive efficaci possono avere un impatto su sicurezza, produttività, costi, qualità, consegne puntuali, inventario e affidabilità delle attrezzature. Le immagini sul posto di lavoro possono giocare un ruolo importante nell’addestramento al lavoro che eliminerà la necessità di una supervisione costante. I dipendenti identificheranno e reagiranno rapidamente ai problemi di sicurezza, qualità ed efficienza. La gestione visiva offre altri vantaggi tra cui:
- Crea stabilità all’ambiente, alle attrezzature e al lavoro svolto.
- Riduce gli errori e gli sbagli.
- Riduce i tempi morti e i costi di manutenzione.
- Aumenta la consapevolezza dei rifiuti e la gestione dei rifiuti.
- Migliora la conformità alla sicurezza.
- Migliora la comunicazione tra i diversi turni.
- Migliora il coinvolgimento e il morale dei dipendenti.
- Elimina la necessità di riunioni che richiedono tempo.
- Rinforza il miglioramento continuo.
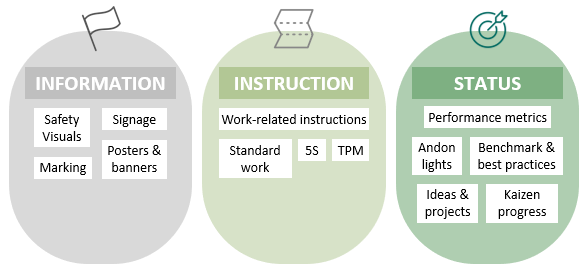
Molte tecniche e principi lean si basano sulla gestione visiva a partire dalla marcatura del pavimento usando nastri adesivi fino ai grandi display e tabelloni. La gestione visiva serve come forza di sostegno chiave per molte tecniche snelle popolari, comprese le 5S, il lavoro standard, la manutenzione produttiva totale (TPM), il cambio rapido e la produzione pull. È particolarmente importante durante la fase iniziale dell’implementazione Lean, quando le aziende usano concetti come 5S e TPM per creare standard e stabilire la stabilità operativa.
- 5S è uno dei principi più fondamentali del Lean. Coinvolge molte attività visive che possono aiutare a creare un ambiente di lavoro migliore. Suggerisce l’uso di colori ed etichette per contrassegnare chiaramente le posizioni di stoccaggio di ogni articolo sul posto di lavoro. Definisce anche i livelli di inventario e i trigger di riordino per garantire che tutto sia disponibile come necessario al punto di utilizzo. Se qualcosa non è normale, vogliamo renderlo il più evidente possibile.
- Le immagini TPM semplificano le attività di manutenzione preventiva assicurando che l’attrezzatura rimanga in condizioni di funzionamento ottimali con guasti minimi. Possono anche essere usati per identificare e prevenire che le anomalie si trasformino in guasti. L’etichettatura e la marcatura dei manometri, dei livelli dell’olio e dei punti di lubrificazione sono tutti esempi di controlli visivi che permettono ai dipendenti di individuare facilmente le anomalie e le condizioni fuori specifica a colpo d’occhio. La prova della trasparenza dell’attrezzatura dovrebbe esistere per facilitare la messa a punto e il controllo. Si raccomanda anche che i registri dei problemi siano usati su ogni macchina.
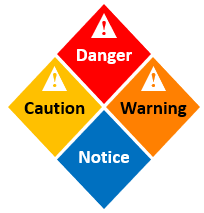
- I controlli visivi di sicurezza sono importanti per mantenere la struttura sicura e rispettosa dell’ambiente. Avvisano i dipendenti e i visitatori dei luoghi e delle situazioni potenzialmente pericolose per prevenire condizioni non sicure. È importante identificare correttamente le attrezzature antincendio, le docce di sicurezza, le stazioni di lavaggio degli occhi, i dispositivi di protezione personale e le stazioni di primo soccorso. La segnaletica, le avvertenze di pericolo e le istruzioni di sicurezza devono essere fornite nel punto di necessità. Tutti gli interruttori di disconnessione per ogni attrezzatura alimentata elettricamente dovrebbero essere chiaramente identificati.
- Un forte sistema di gestione visiva cerca di promuovere la coerenza e creare la stabilità del processo. Le immagini standard del lavoro aiutano a garantire che i compiti siano sempre eseguiti da tutti nel modo più efficiente ed efficace possibile. Includono procedure, istruzioni di lavoro, fogli di controllo, liste di controllo, diagrammi di flusso, programmi, foto e lezioni di un punto. Queste immagini aiutano a minimizzare gli errori di produzione e assicurano che gli standard del posto di lavoro siano rispettati da tutti. Ricorda che le migliori immagini sono quelle che includono foto e/o disegni e quelle che sono collocate nel punto di necessità.
Altre applicazioni:
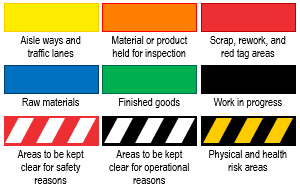
- Marcare il pavimento e il sistema di tubazioni.
- Marcare i materiali e i prodotti in produzione.
- Marcare le macchine, le attrezzature e le linee di produzione.
- Marcare gli uffici, le stanze, le celle e le aree di stoccaggio.
- Segni visivi per aiutare le persone a trovare la strada.
- Segni come “non entrare” e “non fumare”.
- Utilizzare schede codificate a colori e schede Kanban in un sistema pull.
- Utilizzo di tabelle per dare priorità ai problemi e comunicare le contromisure.
- Utilizzo di poster e banner per rafforzare gli obiettivi e i principi Lean.
- Utilizzo di schede di monitoraggio per facilitare la comunicazione in operazioni su più turni.
- Utilizzo di tabelloni per comunicare e monitorare le metriche di processo in tempo reale.
- Utilizzo di tabelloni riassuntivi di produzione per visualizzare informazioni come l’efficienza, il tempo Takt, ecc.
Andon e tabelloni riassuntivi di produzione:
Un display Andon è un sistema di illuminazione multicolore che fornisce un meccanismo semplice e coerente per comunicare informazioni in officina. È uno strumento di comunicazione efficace che porta l’attenzione immediata ai problemi che si verificano in una macchina o in una cella di produzione. Il sistema può includere mezzi per fermare la produzione in modo che il problema possa essere corretto. Per esempio, una luce può accendersi o cambiare colore per indicare una carenza di materie prime o la necessità di manutenzione.
Un posto di lavoro senza un display di metriche di produzione è come una macchina senza tachimetro. Si può sapere dove si sta andando, ma non si ha idea di quando si arriverà. Le schede di riepilogo della produzione sono utilizzate per monitorare l’output del processo e vedere se soddisfa la domanda dei clienti. Le luci Andon e i pannelli di riepilogo della produzione dovrebbero essere visibili in officina per comunicare lo stato attuale di un sistema di produzione. Tutti dovrebbero essere in grado di vedere a che punto è la produzione, il che permette ai team di manutenzione e produzione di risolvere rapidamente i problemi di processo e di qualità che possono verificarsi durante la produzione.
Suggerimenti per creare un sistema di gestione visiva coeso:
- Ricorda che il tuo obiettivo è di rendere l’area più informativa.
- Determina dove hai bisogno di implementare la gestione visiva.
- Decidi chi sarà coinvolto nello sforzo di implementazione.
- Identifica i deficit di informazione, determina cosa deve essere mostrato e il tipo di informazioni che devono essere trasmesse. Un modo è quello di progettare una lista di controllo visiva che copra le posizioni di stoccaggio, il lavoro standard, la sicurezza, la manutenzione, le metriche di processo, i pannelli visivi, ecc.
- Marcare i pavimenti, aggiungere segnali, etichettare le aree di stoccaggio, ecc. Usare gli standard di colore che sono usati in modo coerente nella struttura.
- Le informazioni devono essere facilmente comprensibili, concise, accurate, pertinenti, aggiornate e accessibili a tutti. Tutti devono essere in grado di capire il messaggio.
- Creare una guida che descriva gli elementi chiave associati ad ogni tipo di visual.
Altre informazioni:
- Gestione visiva non è solo rendere visibili grafici e metriche su una parete, è una visualizzazione in tempo reale, ogni ora o giorno, che permette al team di rispondere prontamente ai segnali per risolvere problemi o sostenere il processo produttivo. Questo spesso genera un senso di urgenza nel team e permette di risolvere i problemi sul posto eliminando possibili complicazioni.
- Le metriche di processo devono essere visualizzate sulla macchina o sulla cella di produzione, mentre le informazioni generali dell’impianto devono essere affisse in una posizione centrale dove tutti possono vederle a colpo d’occhio.
- È molto comune condurre eventi Kaizen dove l’obiettivo principale è migliorare la visibilità di una specifica area di lavoro o di un processo. Per esempio, stabilizzare l’ambiente di lavoro usando le 5S, stabilizzare il modo in cui il lavoro viene eseguito usando il lavoro standard, o stabilizzare le prestazioni e l’affidabilità delle attrezzature usando il TPM.